What is the function of applicator material?
Application is the physical process through which a substance (typically a liquid) is spread across a surface or substrate with specific applicator materials. Items that people use each and every day rely on this functionality, including many personal care and cosmetic products, topical applicators for drug delivery, and writing instruments among others. Without an effective means to manage the storage and output of formula, these devices would fail to work properly. The complexity of these solutions can be easily ignored; however, these seemingly basic designs require a sophisticated interplay between different types of porous material components – each performing different functions – in order to produce a dependable system for precise application. At Porex, we apply our material science expertise across fiber, porous plastics, and foam to support precision formula delivery across a variety of industry needs.
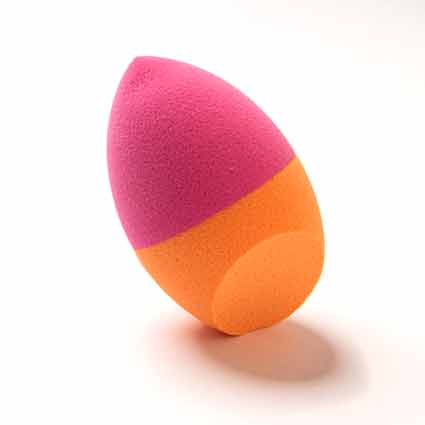

Talk with a Material Science Expert
Webinar
In this webinar preview, explore applicator material as we discuss:
- How an applicator device works
- How to create the right applicator for your use case
- The typical problems that are solved with applicator devices
You’ll learn about the two main markets that benefit from applicator devices, the types of porous polymers needed to create effective applicators, and so much more.
How applicator material works with porous polymers
For an applicator device to work properly, the liquid suspension must deliver to the surface through a phenomenon called capillary action. This is simply the force that facilitates liquid transfer from the reservoir, through the nip/tip, and into the pores of the substrate or surface material. It is important that the surface energy of the liquid suspension be controlled so that the substrate is wettable. To promote wettability, a high surface energy, or strong molecular bond, must be present so that the substrate can pull and retain the formula from the device. Depending on the device and its application, there are many considerations to make when designing your applicator solution, including suspension type, its viscosity, its morphology, the level of flow needed, and the user experience desired.
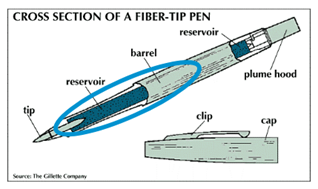
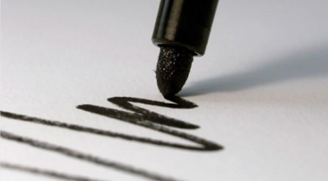
Design challenges solved by applicators
- Delivering the precise amount of liquid or solid onto a surface
- Having the appropriate softness or hardness for the accepting surface (i.e. skin vs. paper or writing board)
- Needing a wispy or rigid applicator tip
- Holding up to repeated uses and application cycles
- Creating a hypoallergenic applicator for skin/body applications
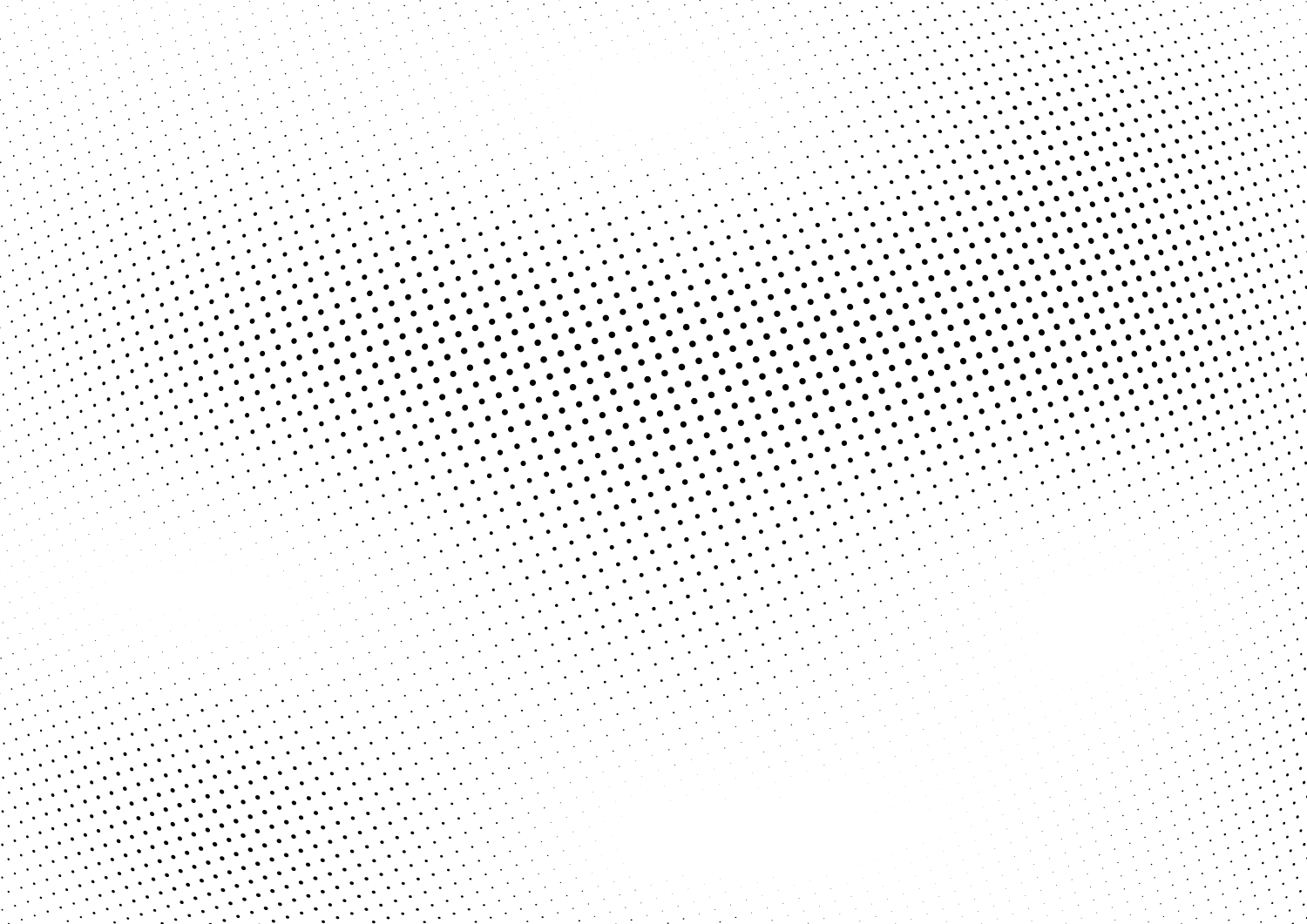
Related Technologies
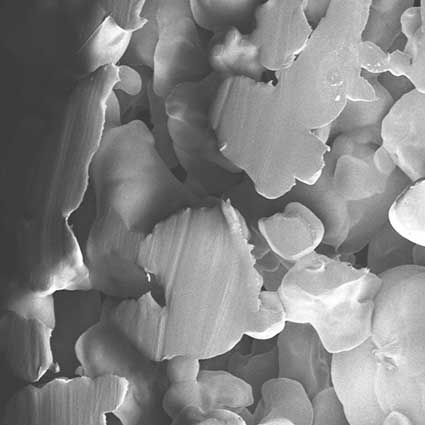
Sintered Porous Plastics
Sintered porous plastics are created using a combination of heat and pressure to bond the materials together.
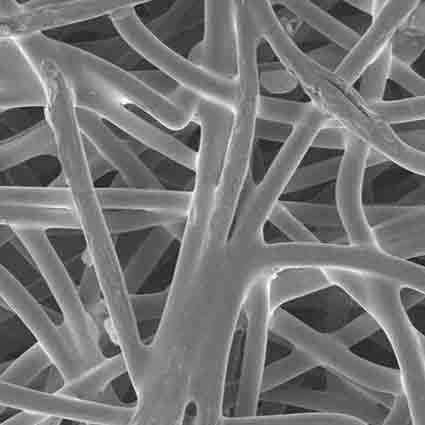
Porous Fiber
Porous fibers consist of bonded fibrous strands which create two-dimensional cross-sections that can be extruded to create three-dimensional shapes.
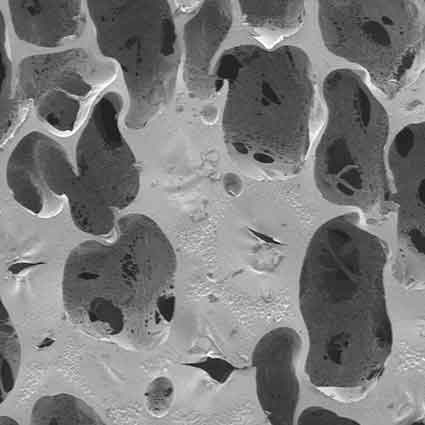
Porous Foam
Our porous foam consists of wide-ranging densities, porosities, and levels of softness for both medical and cosmetic applications.
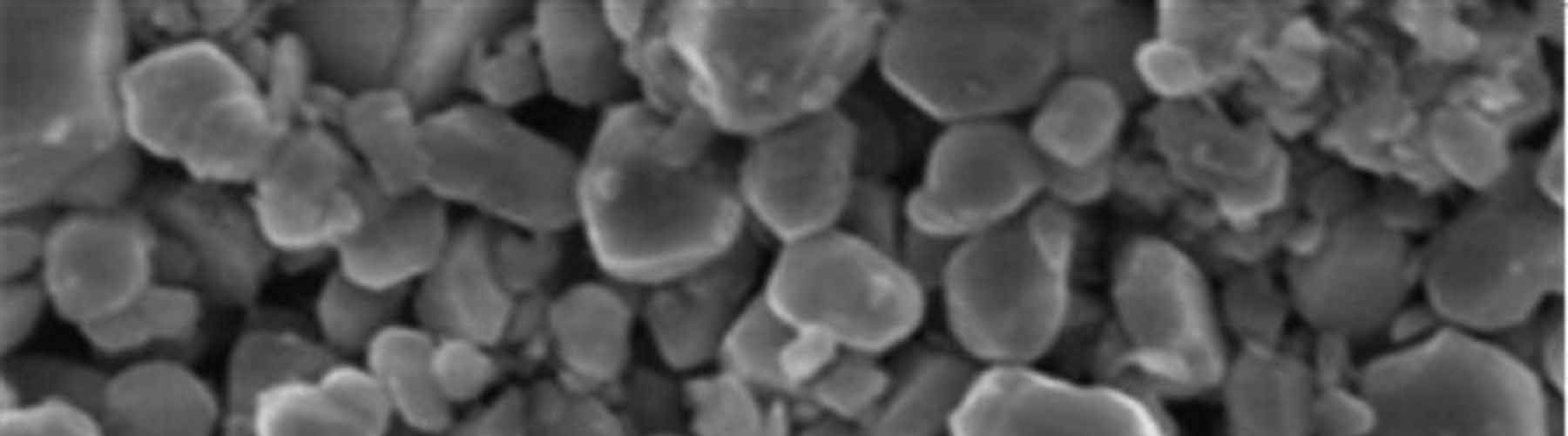
Register for our On-Demand Webinar
Redefining the Capabilities of Foam with Open-Cell Foam