Porous Foam Expertise for Medical & Cosmetic Applications
Open-cell porous foam is manufactured by Porex using proprietary or customized blends of raw materials through a clean polyurethane process that does not use catalysts. Various formulations can offer wide-ranging densities, porosities, and levels of softness available with application-specific additives including antimicrobials, nanomaterials, pharmaceuticals, botanicals, cosmetic ingredients, and colorants that can enhance your device’s look, functionality, and performance. Porex’s porous foam types include both medical-grade (ISO 10993-certified) and cosmetic foams, with pore sizes ranging from 90 microns to over 350 microns.
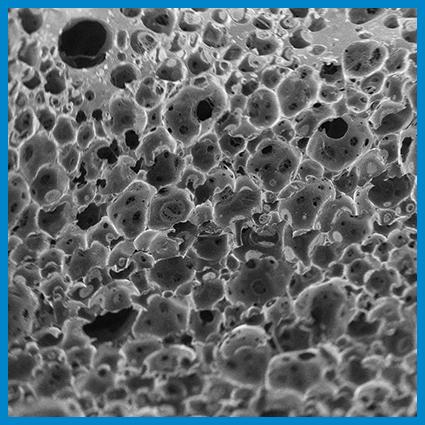

Talk with a Material Science Expert
Manufacturing process
Polyurethane foam materials can be manufactured using two different processes: a conventional “one-shot” process – like you see in furniture and car seat cushions – or as a two-step prepolymer process. During a one-shot approach, all ingredients are simultaneously mixed and poured onto a conveyor, a trough, or a mold, where it is allowed to react, expand and cure. While this process does promote high throughput, it does not lend itself to customization, as cell structures are non-uniform. For application-specific devices, Porex’s two-step process, as highlighted below, allows for the creation of customizable, omnidirectional pores that can promote faster wicking, higher absorption, and excellent retention in both advanced medical and cosmetic applications.
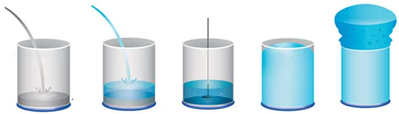
Step 1: Isocyanate, polyol, and/or other ingredients are mixed in a certain stoichiometric ratio to make a prepolymer
Step 2: Prepolymer activated with an aqueous solution containing primarily water.
Step 3: Continuous foaming process from reaction, rising, curing, and drying.
Options for customizing porous foam
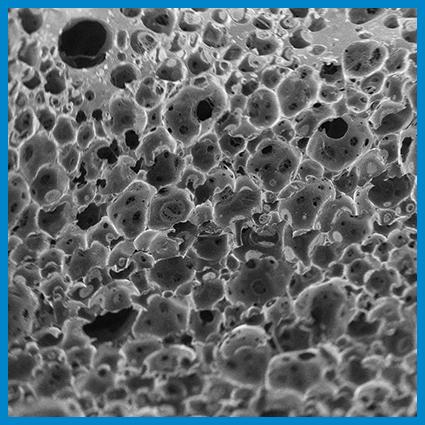
Register for Our On-Demand Webinar
Redefining the Capabilities of Foam with Open-Cell Foam
Common applications for porous foam
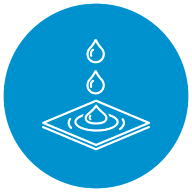
Absorb
Porous foam material can be used in a number of applications requiring absorption such as patient positioning and surgical support as well as PPE face masks and advanced wound care medical-grade foam. Because it is biocompatible, hypoallergenic, and can be customized for softness, it is a good candidate for skin contact.

Apply
For topical skin adhesives or cosmetic makeup sponges, porous foam material can allow for the delivery of precise amounts of liquid, creams, or powder-based foundations without irritating the skin. Porous foam can enable reusability and be made from a bio-based polymer for a more sustainable applicator.
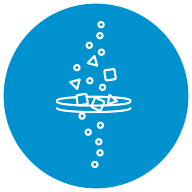
Filter
Filtration properties allow for therapeutic techniques such as using a suction dressing to remove excess exudation while treating acute or chronic wounds or highly sensitive second and third-degree burns. Foam allows the wound edges to be drawn together, reducing the chance of edema and infections. Adding a carbon additive can also help with odor.
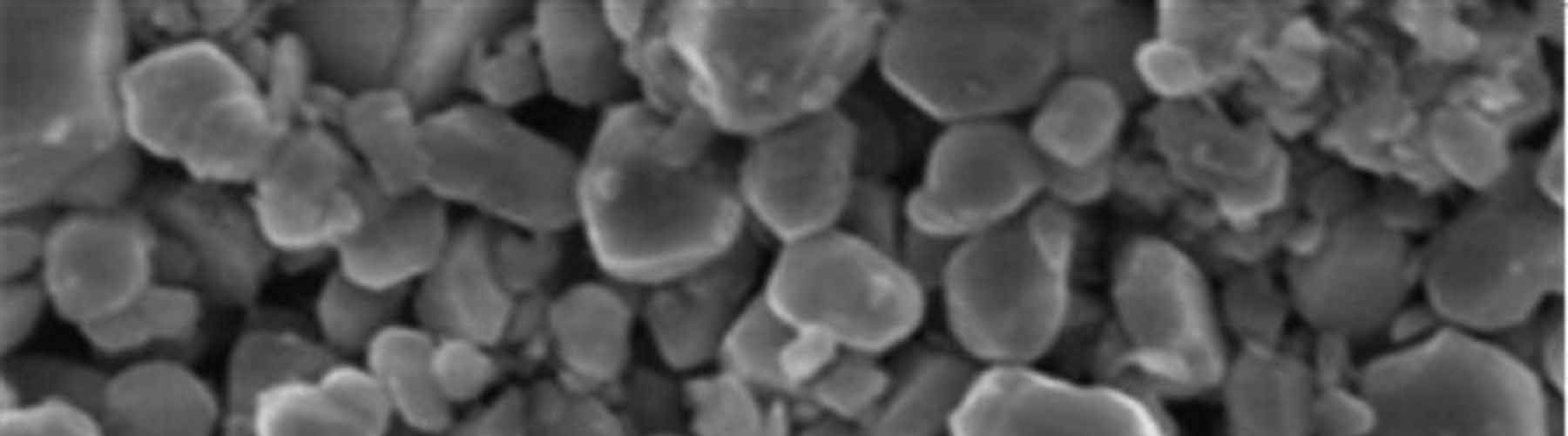
Why do pore size and flow matter?
Learn more in our new technical article
Related Resources
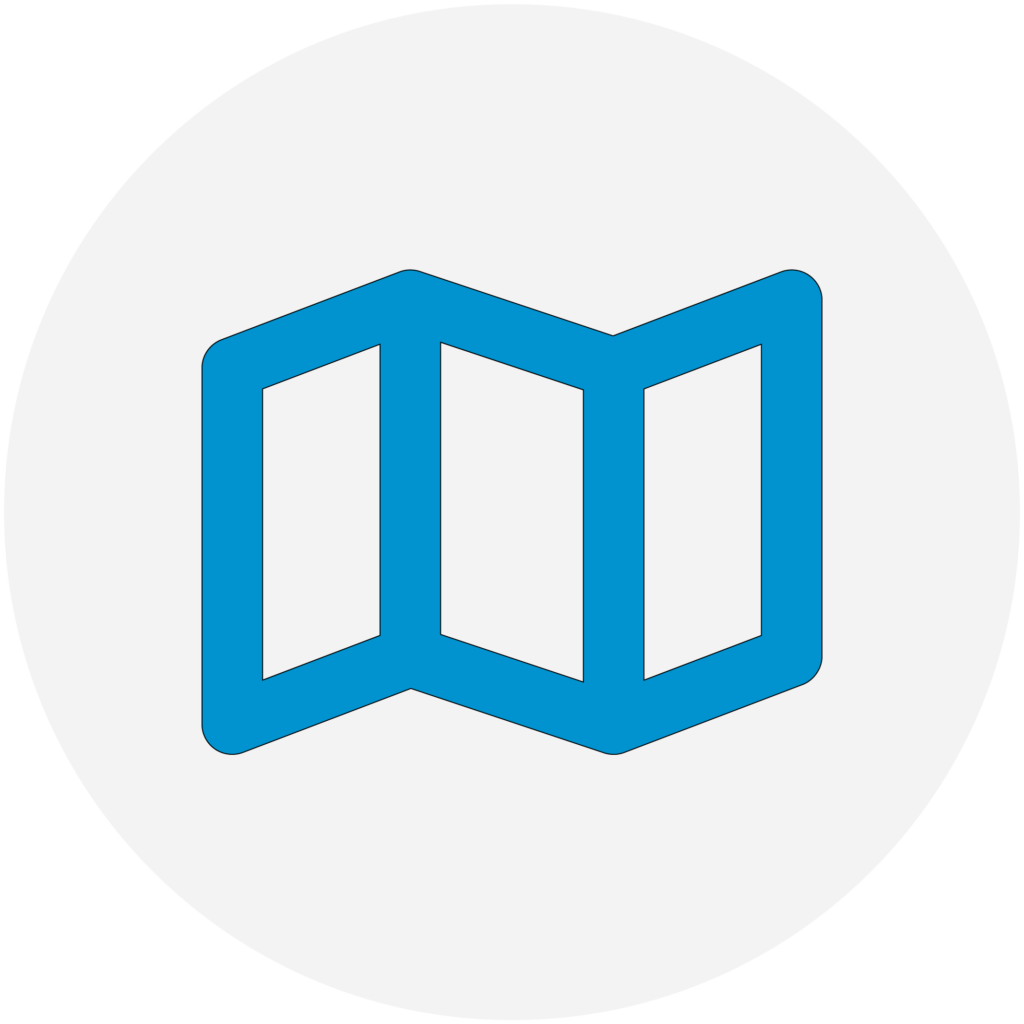
Porex: The Perfect Fit Brochure
Experience Porex’s customizable porous media capabilities. From advanced filtration media to cutting-edge fluid management, our unmatched material science expertise and extensive global manufacturing network help you unlock new frontiers of innovation and efficiency.
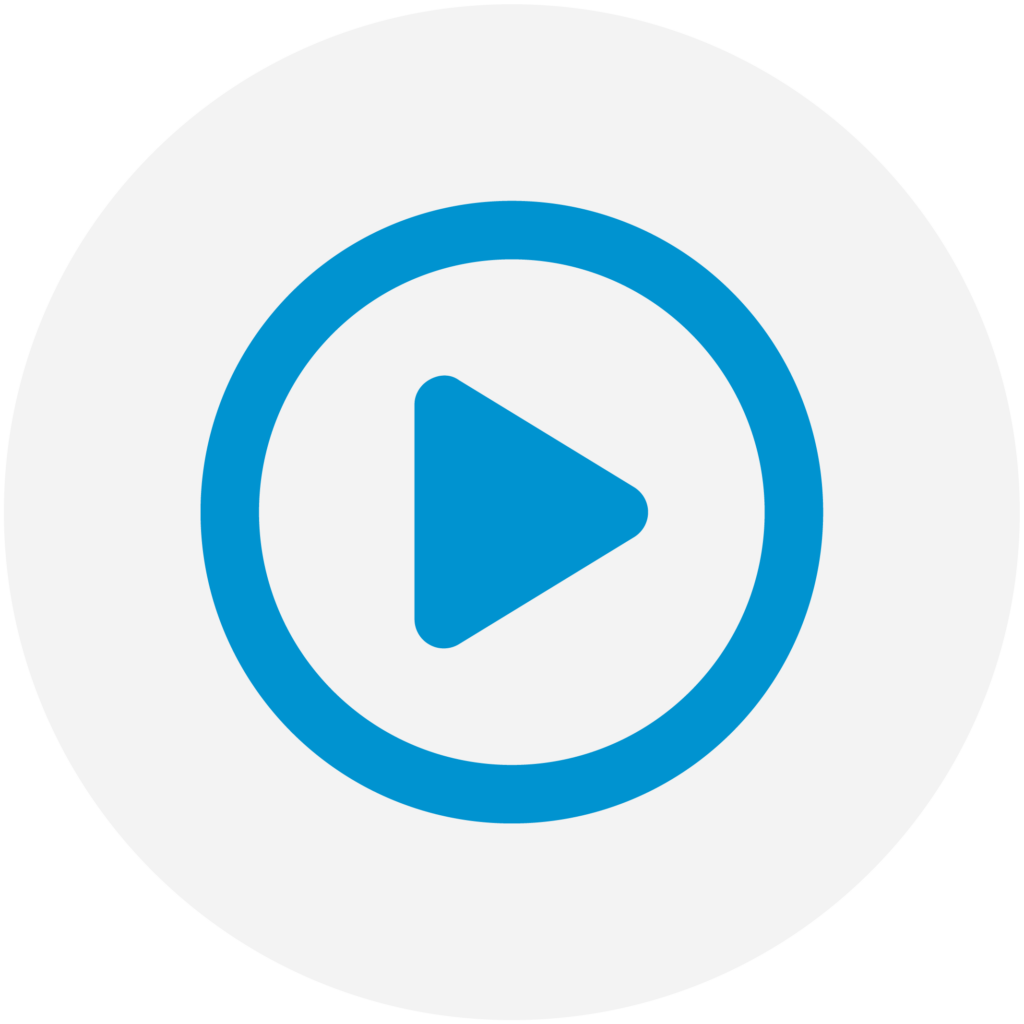
Understanding Pore Size Distribution
In this video, learn how to measure the space between the particles and their effect on component performance.
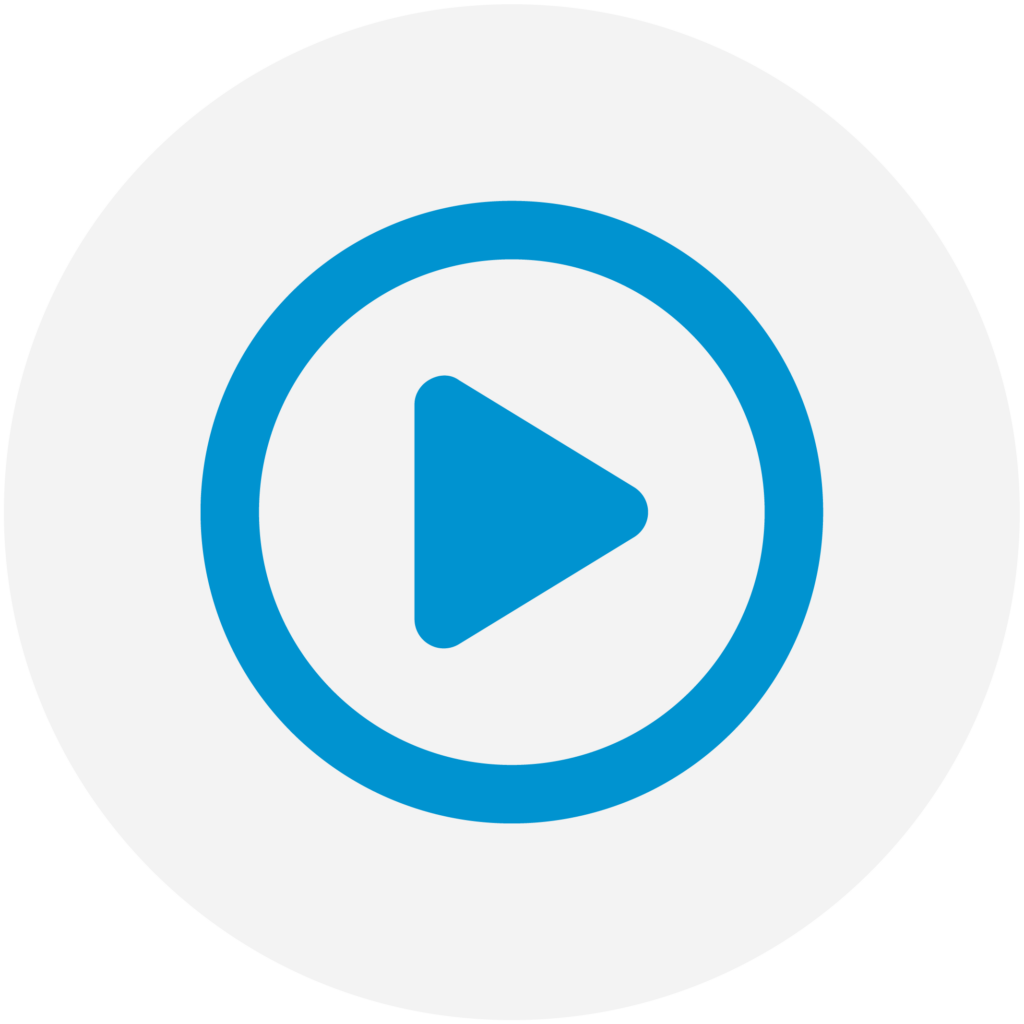
Understanding Pore Volume
Explore the impact of pore volume better to understand its impact on your device’s functionality.
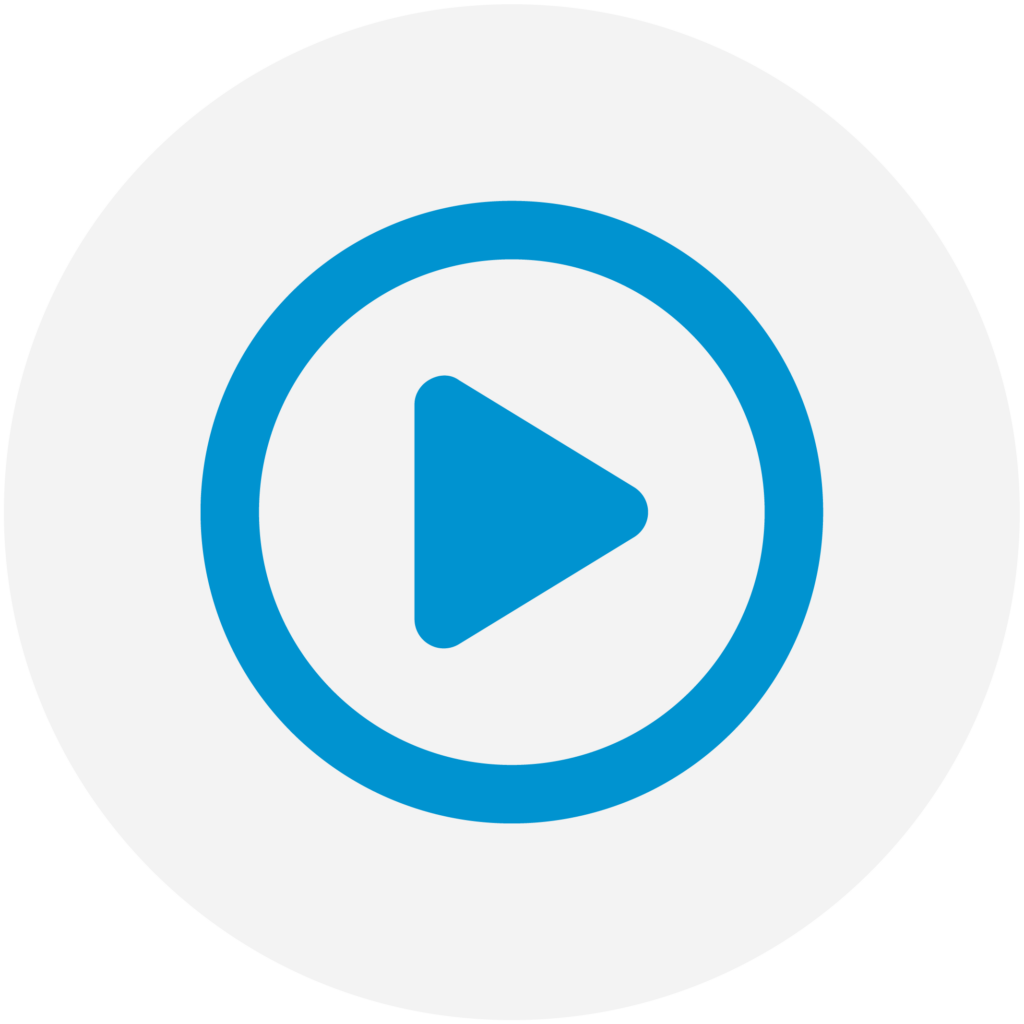
Your Partner in Innovation
Discover how Porex has been a partner in innovation for over 60 years in this video.